Every project site has unique subsurface conditions that must be addressed before construction can begin. Ground improvement solutions can remedy problematic site soils beneath the intended structure to enhance foundation bearing capacity, control settlements and permeability, mitigate liquefaction, reduce lateral spread issues, increase ground density and improve slope stability.
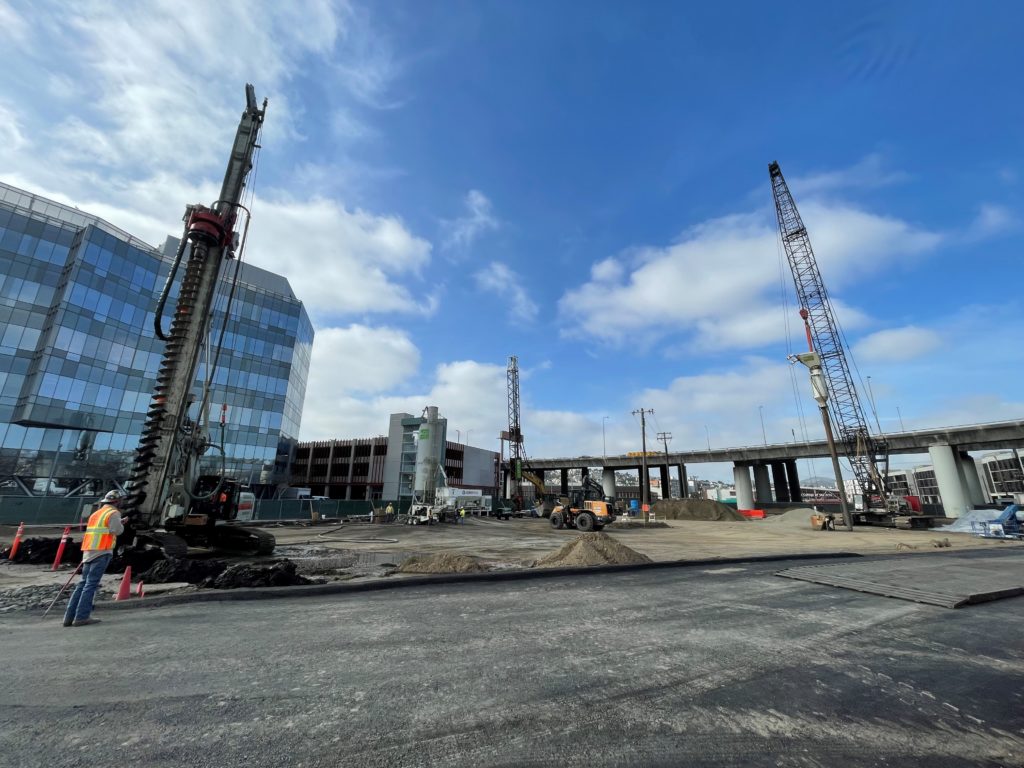
Understanding ground improvement fundamentals can help your design-build be more successful, as can selecting the right ground improvement partner. Read on for ground improvement basics, including the best time to bring in a specialist, decide on ground improvement techniques, how to determine your specific project needs and what to expect from start to finish.
When to Bring in a Ground Improvement Specialist
When is the best time to bring in a ground improvement specialist for a project? Best practices recommend engaging a specialist from the onset of project conceptualization. Crafting solutions at early stages of the project is often most cost-effective in the long run, can support a collaboration of ideas, and ultimately streamline the overall project schedule.
Ground Improvement Techniques
Ground improvement techniques can include technologies such as deep dynamic compaction, jet grouting, cement deep soil mixing, stone columns, aggregate piers, displacement grouting and more. Influential factors in selecting the best technique generally include considerations such as soil type, ground water conditions, project location and project specific design parameters. All of these elements must be assessed when choosing the right approach.
There is a broad spectrum of soil types and ground water condition combinations, and it all comes down to the site-specific constraints when deciding on the right ground improvement technique for an individual build.
The ideal ground improvement technique would be different for a subsurface profile that is predominantly sandy and has a high ground water table and/or is substantially more liquefaction prone, versus a site that has predominantly clayey soil and/or with a low ground water table. For more insight follow the user friendly Feasibility Matrix on our website to get a jumpstart on the best ground improvement technique for your next project.

The order in which deciding on the ground improvement scope and associated design can often be interchangeable i.e., “chicken or the egg” as the scope can influence design decisions and vice versa. Below is a breakdown on how the process can often unfold for illustrative purposes.
How to Determine the Ground Improvement Scope
Working with a partner like AGI makes it easy to determine the right ground improvement technique and scope when beginning a new project. Here’s a high-level breakdown on typical design-build considerations when figuring out the project technique and scope needed to gain the final ground improvement product:
Subsurface Characterization and Overall Development
The first step when determining the technique is to gain an understanding of the subsurface strata and the overall proposed development. The construction manager typically provides the geotechnical report (conveying the subsurface characterization) and overall project drawing set for assessment.
Ground Improvement Scope
Once the engineering recommendations (by others) are established i.e., civil, structural and geotechnical―decisions can be made on the optimal ground improvement technique to be used and associated scope approach.
Methodology is also often driven by considerations such as performance specifications, underground utilities/obstructions, and site access constraints. For instance, gaining access, avoiding utilities and achieving maneuverability in a downtown Los Angeles site with large equipment would be much more challenging than a remote suburban site.
Preliminary Design and Scope Optimization
Once the ground improvement technique and preliminary/conceptual design are conjured (design is discussed in further detail in the following section), schedule and cost related questions come into play. AGI has the right resources to optimize both time and financial constraints, whether it involves working a double shift to speed up the schedule or cut down costs by providing value-engineering solutions. AGI is in a prime position to address a project’s most basic or pressing needs through continuously pushing the envelope of possibility.
Typical Design Process
How does a typical ground improvement design process unfold? Once the ground improvement technique and scope have been tentatively decided the formal design process can begin in conjunction with the project team. While it may vary, here the most common design steps:
- AGI provides a conceptual design based on the ground improvement technique(s) decided. Often times this includes collaborating with the project structural and geotechnical engineer of record and architect to encompass items such as slab/shallow foundation types and loads for the proposed structure, topographic/drainage information from the civil engineer, building geometry data and project-specific constraints.
- In turn, upon receipt and processing of the above data in conjunction with AGI’s own design processes, Issued for Construction (IFC) drawings are stamped by AGI’s P.E. designer and provided to the greater team.
Typical Build Process
Post design, the build process is the execution step of the design-build process before closing out the contract. After the design phase, AGI’s project management team manages schedule, scope, quality expectations and overall proposed site coordination. Once these items are approved, AGI and the client will agree on a construction start date. The sequence of events thereafter are typically as follows:
- AGI mobilizes equipment to the site to begin construction of the approved ground improvement scope of work.
- Quality adherence, regular reporting and open real-time communication are all significant elements to ensure the best project outcomes. During construction, AGI provides quality control (QC) oversight to ensure all installation parameters are met in accordance with IFC drawings. AGI’s site project engineer provides daily field and QC reports to the client’s representative.
- After ground improvement installation is complete and all quality checks are verified, AGI de-mobilizes from the site.
- Leading up to and upon completion of construction work activities, AGI coordinates with the client to close out the project phase. As-built drawings and comprehensive QC documents are provided by AGI for review and acceptance.
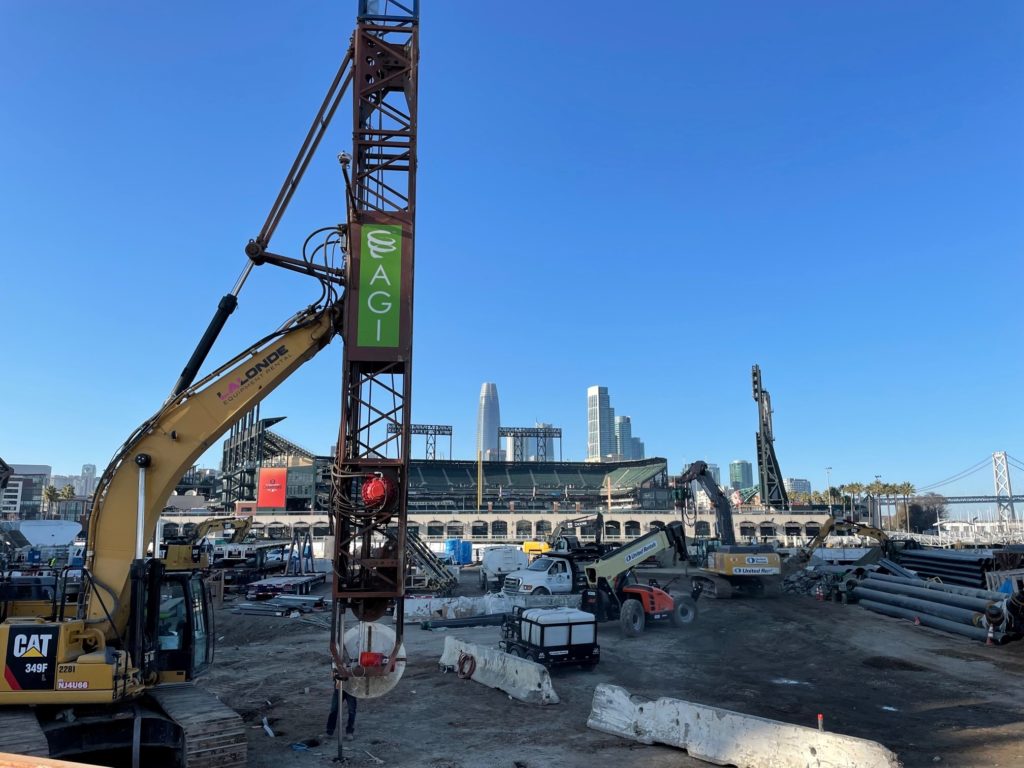
Ground Improvement Success with AGI
Ground improvement for new builds requires expertise with a team dedicated to making the project a success from concept to completion. It can be a complex process that requires the right partner to ensure a successful outcome. AGI is the go-to industry resource for reliable client-tailored ground improvement solutions and a holistic integration through the design-build process. Contact us today to learn how we can develop the ideal ground improvement solution for you. Don’t just take our work for it; hear it directly from our clients.